Our technology explained step by step
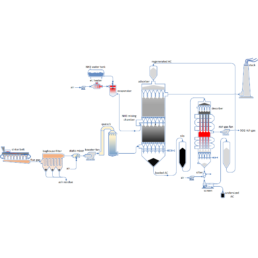
Carbon Selective Catalytic Reduction (CSCR®) is a state-of-the-art technology for waste gas purification of major industrial processes such as steel production, coal fired power plants, waste incinerators and more, with flue gas volumes between 20.000 Nm³/hr and up to 1.800.000 Nm³/hr.
Desulphurisation and denitration of flue gas take place in separated moving beds of activated carbon. Flue gas passes these beds in counter current flow. SOx is codeposited by firstly converting into sulphuric acid and being absorbed in the activated carbon’s pore system. In order to reduce NOx emissions, ammonia is injected into the flue gas stream in a mixing chamber. Due to the properties of activated carbon, CSCR® is able to eliminate nearly all pollutants and contaminants from any flue gas. Next to NOx and SOx also dust, dioxins, furan compounds, mercury and other heavy metals and halogens such as hydrogen fluoride and hydrogen chloride can be separated.
Waste Gas Pretreatment
If necessary, the flue gases temperature will be lowered to 100 °C – 140 °C through means of aeration, water injection or by using heat exchangers.
Dust pollution is taken care of by a baghouse or electric filter.
It is also possible to remove highly corrisive media such as HCl, HF and SO3 with the injection of Ca(OH)2. Thus, subsequent equipment is protected from corrosion and prevented from falling below the acid dew point.
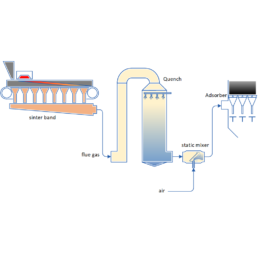
Booster fan
Depending on the field of application, on the waste gas pretreatment as well as on the design of the CSCR®-Adsorber, fans with a pressure drop between +2000 Pa and +8000 Pa are being used.
CSCR®-Plants are being designed for flue gas flow rates between 2,000 Nm³/h to 1,800,000 Nm³/h. For each individual case there are special requirements for the booster fan.
CSCR®-Adsorber
The core of every of our waste gas purification plants is the CSCR®-Adsorber. It consists of several, up to 64, single modules, where the flue gas is being cleaned. Depending on the requirements, the flue gas is being led through one or two moving beds of active carbon, counter flow wise. Following pollutants can be seperated:
– SO²
– NOx
– Dust
– Heavy Metals
– Mercury
– Halogens such as HCl and HF
– Dioxins and furan compounds
For the seperation of NOx, gaseous ammonia is being mixed into the flue gas stream. Substantial differences between CSCR® and other processes based on active carbon is the operation in counter flow. Active carbon flows slowly from top to bottom whereas flue gas flows from bottom to top. The advantage is that only fully loaded active carbon leaves the adsorber at the bottom. Thus the working capital requirement is much lower compared to other active carbon processes.
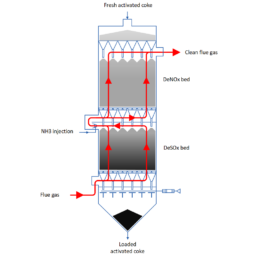
Ammonia system
In order to separate NOx, ammonia NH³ (or any gas able to reduce NOx) is used. A mixture of ammonia and water will be evaporated and mixed with air. The produced ammonia-water-air-mix is equally distributed to all modules. In specially designed mixing chambers these mixture is added to the flue gas stream to ensure thorough mixing.
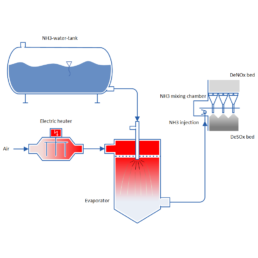
Conveying system
Loaded active carbon is discharged from the adsorber modules and conveyed with bucket elevators to intermediate bunkers. Subsequently it is transported to the regeneration plant, which we call the desorber. After regeneration active carbon is being cleaned of dust and fine particles and conveyed to another intermediate bunker before being led to the adsorber. Great importance is attached to the gentle conveying of active carbon in order to further reduce wastage.
Regeneration
Loaded activated carbon can be regenerated using thermal treatment. The active carbon is being heated inside a desorber to up to 450 °C. At these temperatures, previously adsorbed substances are desorbed and destroyed by thermal decomposition. The resulting rich gas is collected and discharged. It can be further processed to produce sulfuric acid, fertilizer or elemental sulfur. After the heating zone in the desorber follows the residual degassing zone. Finally the active carbon will be cooled down. By means of special contruction comparable to a tube and shell heat exchanger the active carbon never enters into contact with heating gas or cooling air.
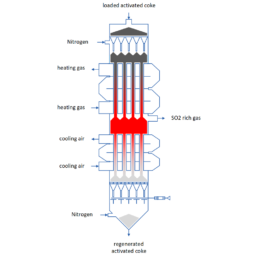