CSCR®
CSCR® (Carbon Selective Catalytic Reduction) is a dry flue gas purification system.
Flue gas flows through one or more activated coke beds in a modular Adsorber.
The modules are designed to enable a counterflow-process. This results in higher process efficiency and economic advantages.
The technology was developed and patented by Dr. Grochowski.
CSCR® in numbers
Plants worldwide: | >80 |
---|---|
Flue gas volumes: | 2,000 Nm³/hr … >2,000,000 Nm³/hr |
Flue gas temperature: | 90°C – 140°C |
Removal efficiencies: | SOX >90% NOX >60% Dioxins/Furans >99% Hg >90% Heavy metals >80% Dust >80% H2S >80% |
Operating materials: | Activated coke (heat furnace coke or formed activated coke), Ammonia (for de-NOX). |
Special features: | Moving bed Adsorber with activated coke in counter-current operation. |
QUALITYFORSUSTAINABILITY
1. Preconditioning
Preconditioning stages are typically used to reduce acidic components to prevent corrosion problems. Other pretreatment components may include dust collectors and temperature control.
2. Fan
A booster fan (axial or radial) generates the necessary pressure increase of up to 6000 Pa for operation.
3. Adsorber
In the Adsorber, the flue gas is devided into up to 64 modules, depending on size of plant. Here, the flue gas flows through one or more activated coke beds from bottom to top. In the process pollutants are adsorbed by the activated coke and/or chemically converted into less harmfull compounds and deposited in the pores of activated coke. Loaded activated coke is discharged, collected and transported to the desorber (point 5) for regeneration.
4. Silos
Fresh activated coke is stored in silos and is automatically fed into the system to compensate for activated coke losses.
5. Desorber
Above a certain activated coke circulation rate, it is economical to regenerate activated coke directly on site. Depending on the plant concept, this is done in one or more desorbers. Here, activated coke is thermally regenerated. The resulting rich gas contains high concentrations of SO2.
6. Screen
In order to keep the pressure drop in the Adsorber within an optimum range, the activated coke is screened after regeneration. Activated coke granules below a certain size are separated.
7. SO2-Rich-gas
The rich gas produced during regeneration of the activated coke is usually further processed in a separate plant to either sulfuric acid, ammonium sulfate or elemental sulfur.
8. NH3 System
For NOX removal, gaseous ammonia is added to the flue gas. It is obtained by evaporation of ammonia-water.
9. Conveying System
Loaded activated coke is transported from the Adsorber to the Desorbers. Regenerated activated coke is then transported back to the Adsorber. Special transport systems are used to minimize activated coke losses and wear caused by abrasion.
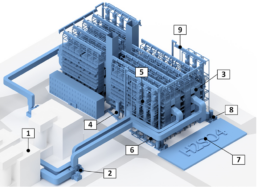
1. Preconditioning
Preconditioning stages are typically used to reduce acidic components to prevent corrosion problems. Other pretreatment components may include dust collectors and temperature control.
2. Fan
A booster fan (axial or radial) generates the necessary pressure increase of up to 6000 Pa for operation.
3. Adsorber
In the Adsorber, the flue gas is devided into up to 64 modules, depending on size of plant. Here, the flue gas flows through one or more activated coke beds from bottom to top. In the process pollutants are adsorbed by the activated coke and/or chemically converted into less harmfull compounds and deposited in the pores of activated coke. Loaded activated coke is discharged, collected and transported to the desorber (point 5) for regeneration.
4. Silos
Fresh activated coke is stored in silos and is automatically fed into the system to compensate for activated coke losses.
5. Desorber
Above a certain activated coke circulation rate, it is economical to regenerate activated coke directly on site. Depending on the plant concept, this is done in one or more desorbers. Here, activated coke is thermally regenerated. The resulting rich gas contains high concentrations of SO2.
6. Screen
In order to keep the pressure drop in the Adsorber within an optimum range, the activated coke is screened after regeneration. Activated coke granules below a certain size are separated.
7. SO2-Rich-gas
The rich gas produced during regeneration of the activated coke is usually further processed in a separate plant to either sulfuric acid, ammonium sulfate or elemental sulfur.
8. NH3 System
For NOX removal, gaseous ammonia is added to the flue gas. It is obtained by evaporation of ammonia-water.
9. Conveying System
Loaded activated coke is transported from the Adsorber to the Desorbers. Regenerated activated coke is then transported back to the Adsorber. Special transport systems are used to minimize activated coke losses and wear caused by abrasion.
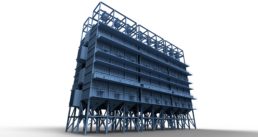
Business Model
For international projects WVK partners with experienced companies (Licensee), which are familiar with the local aspects of the projects. Within the framework of this partnership, WKV assumes the following roles:
– Licensor for CSCR® and know-how transfer to the Licensee.
– Concept Engineering, Basic Engineering and part of the Detail Engineering
– Supporting the Licensee through supervision from construction, assembly and commissioning on site.
Through the extensive knowledge transfer WKV enables its licensees to represent the WKV technology/CSCR® in the market. WKV supports licensees in all project phases, starting with the pre-project phase up to after-sales support.
Since 1967, Dr. Horst Grochowski has pioneered the world’s first industrial waste gas purification using activated coke. Initially, he developed the cross-flow Adsorber together with the German Bergbauforschung (Coal Mining Research Institute). In 1986, Dr. Grochowski founded the engineering company WKV and further developed the crossflow Adsorber to the counterflow Adsorber. This patented technology has since been known as WKV-Technology/CSCR® (Carbon Selective Catalytic Reduction) and is used worldwide. By 2021, a total of more than 80 plants had been installed worldwide.
The WKV-Technology / CSCR® (Carbon Selective Catalytic Reduction) is used worldwide in a wide range of industries, including:
Power plants |
---|
Steel industry |
Cement plants |
Household waste incineration |
Industrial waste incineration |
Sewage sludge incineration |
Chemical industry |
LCD Glass melting |
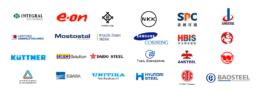
Selected references
Waste Incineration Plant EbS Wien, Austria
Plant type:
Lines: 2x Rotary Kiln, 4x Fluidized Bed Incineration for household waste
Flue Gas Volume Flow:
546,000 Nm³/h
AC-Type:
HOK
Main purpose of CSCR®:
Removal of SOX, Dioxins, Hg, Heavy Metals and Dust.
Data
Inlet | Outlet | Regulation | Unit | |
SO2 | 1400 | 0.2 | 50 | mg/Nm³ |
NOX | - | - | 200 | mg/Nm³ |
Dust | 15 | 3 | 10 | mg/Nm³ |
Hg | 0.65 | 0.01 | 0.05 | mg/Nm³ |
HCl | 1800 | 0.1 | 10 | mg/Nm³ |
HF | 40 | - | 1 | mg/Nm³ |
Dioxin | 20 | 0.002 | 0.1 | ngTEQ/Nm³ |
LCD Glass Plant, Samsung Corning, Cheonan, Korea
Plant type:
LCD Glass Production
Flue Gas Volume Flow:
60 plants with each 18,000 – 75,000 Nm³/h
AC-Type:
FAK
Main purpose of CSCR®:
Removal of NOX and inorganic compounds.
Data
Inlet | Outlet | Unit | |
SO2 | 55 | 8 | mg/Nm³ |
NOX | 470 | 150 | mg/Nm³ |
Dust | 5 | 2.5 | mg/Nm³ |
Hg | 1.3 | 0.8 | mg/Nm³ |
Dioxin | 0.14 | 0.1 | ngTEQ/Nm³ |
LCD Glass Plant, Samsung Corning, Cheonan, Korea
Plant type:
LCD Glass Production
Flue Gas Volume Flow:
60 plants with each 18,000 – 75,000 Nm³/h
AC-Type:
FAK
Main purpose of CSCR®:
Removal of NOX and inorganic compounds.
Data
Inlet | Outlet | Unit | |
SO2 | 55 | 8 | mg/Nm³ |
NOX | 470 | 150 | mg/Nm³ |
Dust | 5 | 2.5 | mg/Nm³ |
Hg | 1.3 | 0.8 | mg/Nm³ |
Dioxin | 0.14 | 0.1 | ngTEQ/Nm³ |
Sinter Belt, Hyundai Steel, Korea
Plant type:
Steel Production with Sinter Belt
Flue Gas Volume Flow:
1,400,000 Nm³/h
AC-Type:
FAK
Main purpose of CSCR®:
Removal of SOX and NOX.
Data
Inlet | Outlet | Regulation | Unit | |
SO2 | 630 | 13 | 115 | mg/Nm³ |
NOX | 450 | <80 | 80 | mg/Nm³ |
Dust | 40 | <10 | 10 | mg/Nm³ |
Hg | 0.3 | 0.05 | 0.1 | mg/Nm³ |
Dioxin | 3 | 0.05 | 0.1 | ngTEQ/Nm³ |
Sinter Belt, Handan Steel Corporation (HBIS Group), Hebei, China
Plant type:
Steel Production with Sinter Belt
Flue Gas Volume Flow:
1,600,000 Nm³/h
AC-Type:
FAK
Main purpose of CSCR®:
Removal of SOX and NOX.
Data
Inlet | Outlet | Regulation | Unit | |
SO2 | 700 | < 10 | 35 | mg/Nm³ |
NOX | 250 | < 50 | 50 | mg/Nm³ |
Dust | 50 | <10 | 10 | mg/Nm³ |
Hg | 0.3 | 0.1 | - | mg/Nm³ |
Dioxin | 3 | 0.1 | 0.5 | ngTEQ/Nm³ |
Sinter Belt, Handan Steel Corporation (HBIS Group), Hebei, China
Plant type:
Steel Production with Sinter Belt
Flue Gas Volume Flow:
1,600,000 Nm³/h
AC-Type:
FAK
Main purpose of CSCR®:
Removal of SOX and NOX.
Data
Inlet | Outlet | Regulation | Unit | |
SO2 | 700 | < 10 | 35 | mg/Nm³ |
NOX | 250 | < 50 | 50 | mg/Nm³ |
Dust | 50 | <10 | 10 | mg/Nm³ |
Hg | 0.3 | 0.1 | - | mg/Nm³ |
Dioxin | 3 | 0.1 | 0.5 | ngTEQ/Nm³ |
Get in contact
We are available for you